Infrastructure
Jayashree has got well equipped state-of-the-art Tool Design, Tool Room, Molding and Extrusion facility to cater high volume production requirements of all type of Rubber products.
Design Development
The Company has the backing of a very strong R & D center and test lab in Pune City consisting of professionals qualified in Rubber Technology & Engineering & Validation Research with state of the art Software & Hardware for Design & simulation.
Our Technocrats in R& D dept is continuously striving for new product development, improvement in existing products , Formulations for new rubber materials, cost reductions and import substitution of Automotive Parts and Components by adopting advanced technology and designing capabilities. Hence, it is recognized and registered as a research institute by Department of Scientific & Industrial Research (DSIR), Ministry of Science & Technology, Government of India in 2015. We are one of the very rubber component manufacturer in India having this government recognition for the R&D centre.
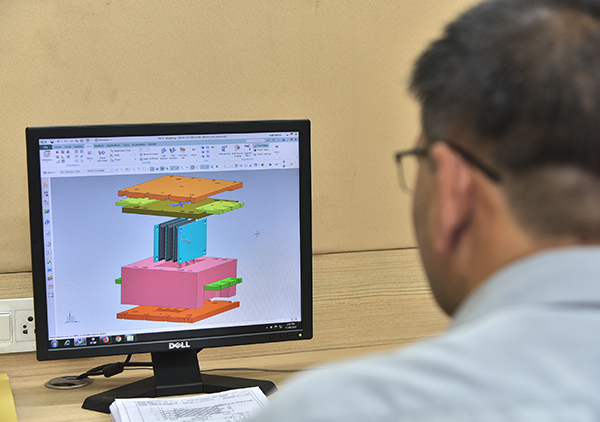
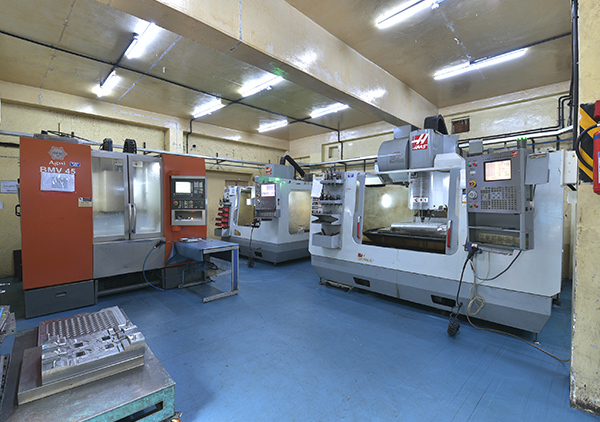
In-House Tool Room
Equipped with latest CNC machineries, our die making capability is one of the best in the country for Rubber Industry.
Innovative design, best machineries and craftsmanship work in harmony to achieve perfection in tool making. We design and develop 125 – 150 multi cavity tools annually. Our in-house tool room help us to serve our customers with quick delivery.
Rubber Mixing
The most critical process in rubber product manufacturing is mixing process. Jayashree has got the strong know-how on formulations & Mixing Technology which is acquired by the company over a period of time . The mixing is done by using dispersion Kneader and open roll mixing mill technology. The Dispersion Analyzer will ensure the quality of carbon dispersion in the mixing process. We are processing all type of synthetic rubbers & Natural Rubber in our mixing plant. We have implemented robust system & process flow in our RM storage & Mixing plant through our Japanese Consultant. We can design & develop any international customer specifications for Rubber compounds. Jayashree has got 3 mixing plants in India , 2 in Pune & one in Haridwar & the combined installed mixing capacity of 72,000MT /annum. The 3rd Mixing plant started in Pune in 2018 is a state-of-the art world class automated mixing plant.
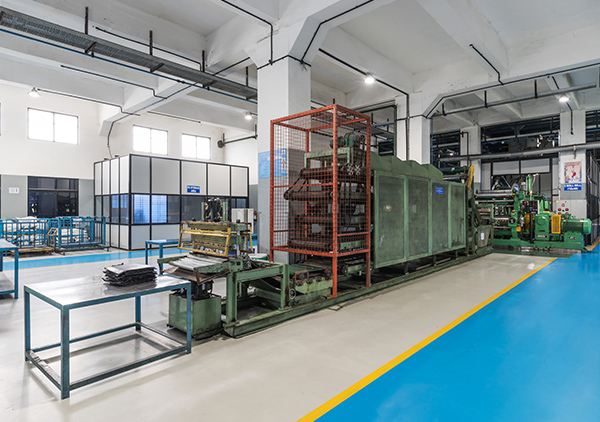
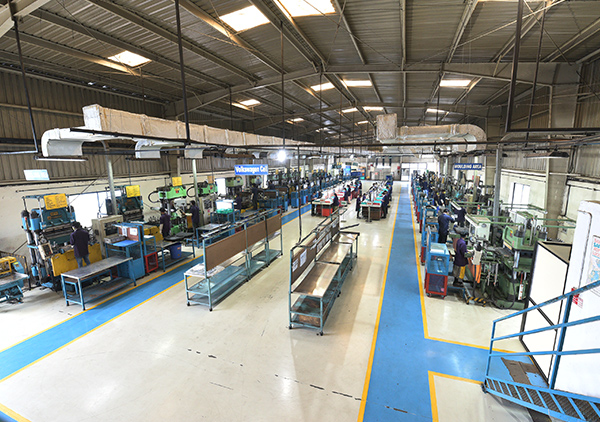
Rubber Molding
We have been producing different type of runner molded components in synthetic runner as well as natural rubber. Jayashree has got the expertise in molding the polymers like EPDM, NBR, NEOPRENE, SILICONE, FLURO SILICON, VITON(FKM) , ACM, AEM(VAMAC) , SBR, NATURAL RUBBER. We do produce molded parts by using compression molding, transfer molding and rubber injection molding process. In injection process we can do cold rubber as well as hot rubber technology to save material and increase productivity. We are one of the few companies in India who successfully developed Radiator Gaskets for global OEMs by meeting the stringent sealing requirement and excellent process consistency. Special controlled processes are developed by Jayashree to produce such high performance products.
Rubber Extrusion
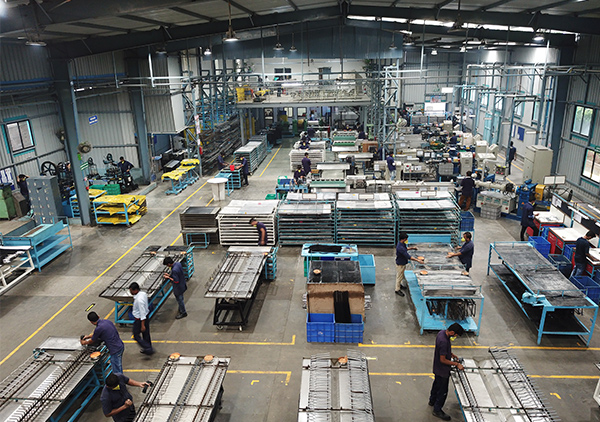
Fuel Tube
Fuel Tubes are mainly used in motorcycles for carrying fuel from carburetor to engine. Other applications include transfer of fuel from fuel tank to carburetor, as breather pipe, over flow pipe, etc. our single & double layered fuel tubes meet the stringent requirements of low and high temperatures making them shrink proof, heat resistant and highly durable. Available in several colors, our fuel tubes provide the perfect solution for diesel and petrol automobiles and generators.
We use polymers such as NBR-PVC, NBR, ECO, HNBR in the inner layer thus ensuring immense fuel resistance and fuel impermeability. Chloro-sulfonated Polyethylene (Hypalon/CSM) & CR used in the outer layer provide excellent ozone resistance. Manufactured with precision and high quality standards. Heat shield can be provided as per requirement. These tubes can be customized to different Outer Diameter (OD) and Inner Diameter (ID) for Petrol, Diesel, CNG, LPG and Vaccum Pipes.
Microwave Extrusion Lines
In order to support our automotive customers different application, we have introduced extruders with online microwave curing system in Jayashree in 2001.
Today we have 2 Microwave lines & producing various rubber profiles in solid & sponge Rubber. We also produce dual layer profiles with sponge & solid rubber which are used in 2 wheelers seat sealing applications.
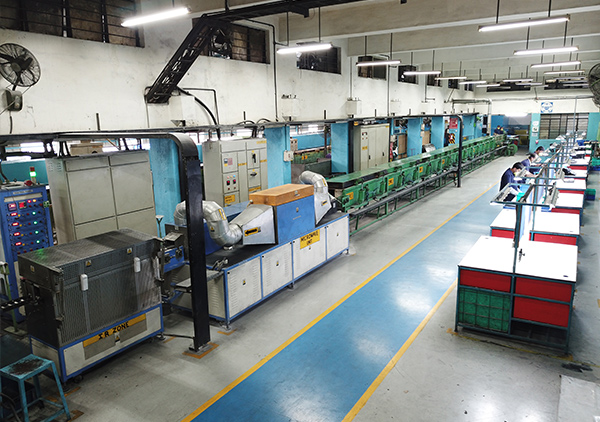
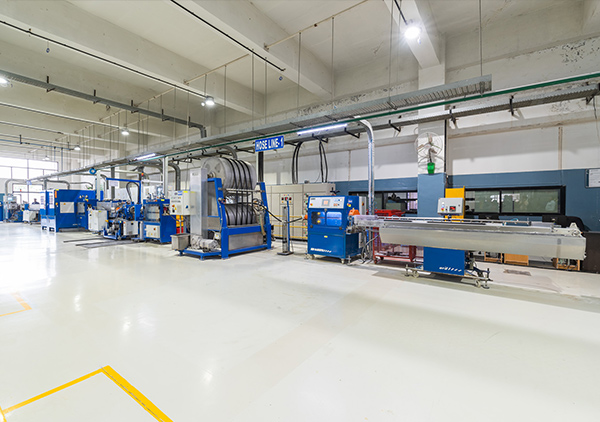
Hose production Line
Jayashree Polymers is in the business of rubber multi layer hoses for the last 15 years.
We have started a new Hose Plant in Chakan Industrial area in 2012 with a state-of-art sophisticated extrusion line from Germany. With the introduce of this new extrusion line from Europe, Jayashree group has given a new dimension to the hose manufacturing technology in India. The line is equipped with co-extrusion facility for innner layer, Knitting & Spiral Braiding technology apart from the Cross head extruder & drum cooling system. We are supplying our multi layer hoses to many Automotive OEMs in India & overseas. We produce Radiator, Heater, Water, Vacuum, EGR, DPF, CAC, Turbo, Fuel application hoses from this line.
Silicon Hoses Extrusion Lines
Jayashree Polymers make variety of silicon hoses in the dedicated plant at Chakan Industrial area in Pune city for 4 years. The silicon line is equipped with latest 3 roll calendaring machines, BIAS cutting machines, Semi Automated Wrapping machines, Hot Air Oven , Steam Vulcanization system & well trained man power. Silicon Hoses are made with Polyester / Nylon or Aramid Fabric in single ply to 5 play depending on the application and customer specifications. The silicon hoses are highly resistant to hardening, good compression set & ozone resistant . Our Silicon hoses have very long life & hence reducing maintenance problems in field.
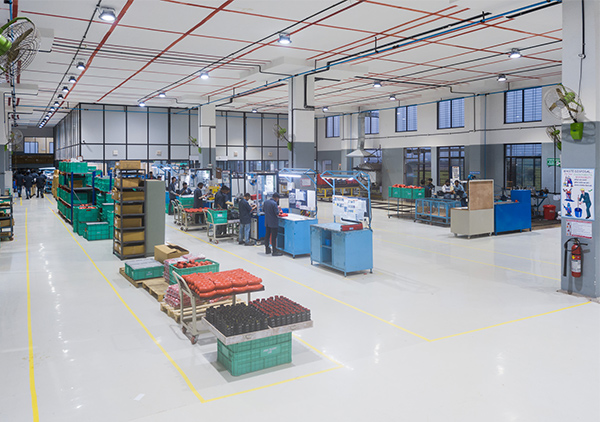
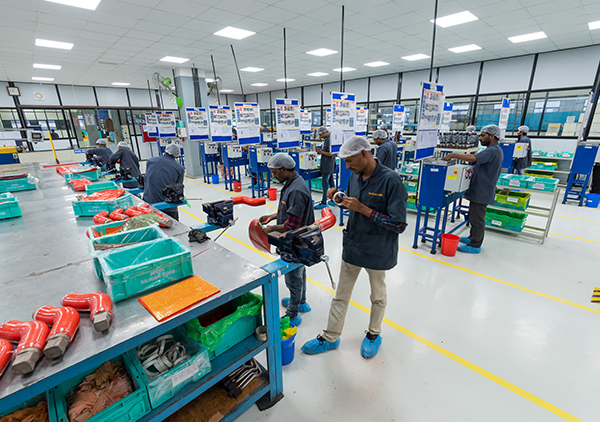
Silicon Hoses Manual Build Line
Apart from extruded hoses, we produce SILICON Hoses with manual building process.
We are equipped with calendaring machines & well trained man power to facilitate Silicon Hose production process.
Hoses with operating temp up 250 Degree. | Hoses with operating temp up 250 Degree. |
2/3/4 Ply reinforcement hoses. | 2/3/4 Ply reinforcement hoses. |
Metal Tube Assemblies & Flexible Hose Assemblies
Jayashree group has ventured into the business of Tubular products in 2011 by starting a state-of-art plant at Chakan industrial area in Pune.
In short span of 7 years, Jayashree has made substantial head way in this product line by start supplying major auto OEMs in India.
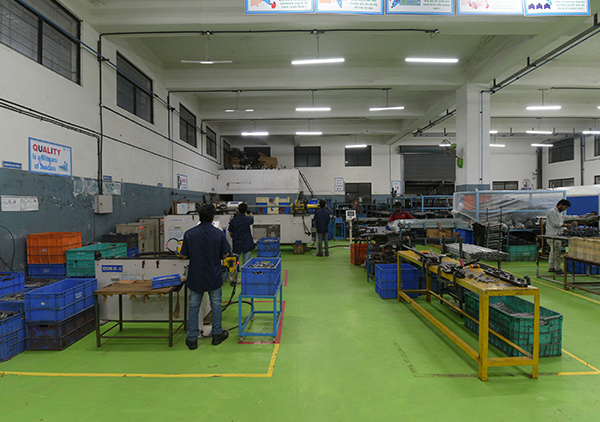
Highlights of our Manufacturing facilities for tubular components
CNC Bending Machines from Japan | Brazing & Welding Line |
Can Handle tubes ID from 6mm to 100mm | Leakage Testing Machine upto 700 bar |
Crimping machines from FIN POWER | Clean Room as per Delphi Class 100,000 |
End Forming Machines | Indore to Hosur |
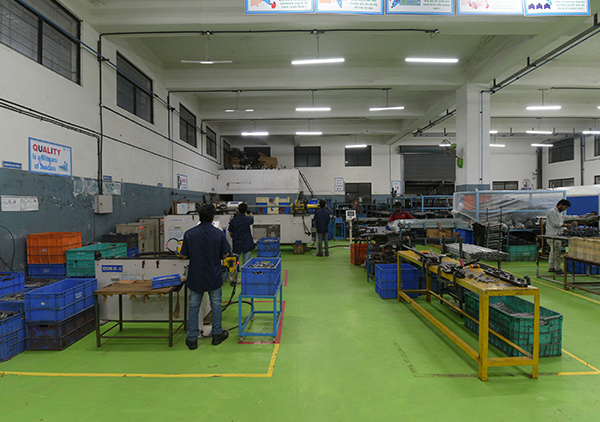
CNC Bending
Equipped with latest CNC machineries, our die making capability is one of the best in the country for Rubber Industry.
Innovative design, best machineries and craftsmanship work in harmony to achieve perfection in tool making. We design and develop 125 – 150 multi cavity tools annually. Our in-house tool room help us to serve our customers with quick delivery.
Nylon Tube Assy Foming
We produce Nylon tube forming and assemblies with Quick Fix Connectors(QFC) and produce Fuel Lines for 4 wheeler industry as well as 2 Wheeler industry. The Nylon tube forming is done though hot air oven as well as steam vulcanizing process . The tubes are sourced from reputed manufactures from India/ aboard based on specifications like mono layer , multi layer, corrugated and braided Poly Amide tubes. We use cold insertion technique to assembly of PA-12 tubes with connectors.
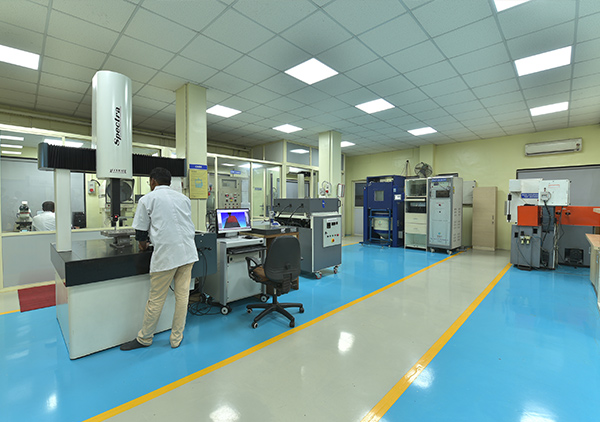
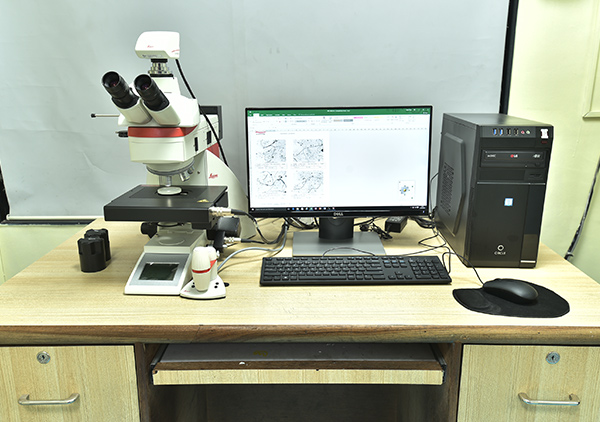
Laboratory & Testing Equipments
Jayashree has got well equipped laboratory in all the production plants. Also, we have a centralized R&D at our Plant-III at Pune for the validation of Raw materials & End products.
We have a wide range of equipment installed in-house which ensures the right quality products as per the customer specifications & performance requirements. We have well qualified and experienced technical staff at R&D Centre and respective production plants and the systems are synchronized in such a way that information are shared quick as possible to fix technical concerns from each plants.
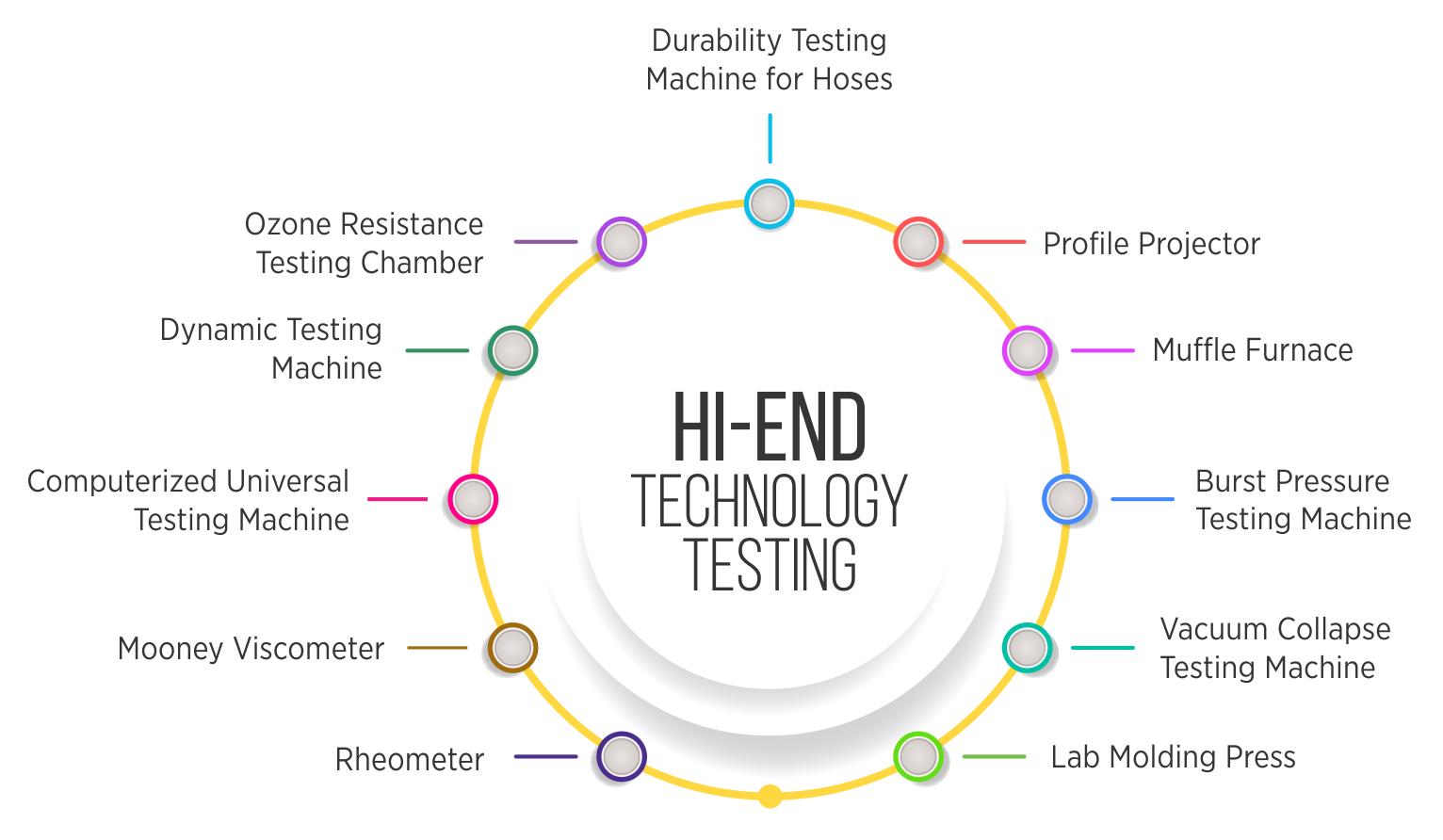